 |
Нередко задача производственного учета и калькуляции себестоимости изготавливаемых изделий ассоциируется у экономических служб большинства российских промышленных предприятия с неким «Бермудским треугольником». Проблемой является правильное вычисление производственной и полной себестоимости продукции ради установления действительной прибыльности отдельных выпускаемых продуктов. Традиционный финансовый учет только запутывает ситуацию, поскольку согласно ему на завод поступал поток ресурсов, которые исчезают в этом «Бермудском треугольнике»: растворившись в хитросплетении технологических потоков между цехами, проходя ряд подразделений, возвращаясь назад, разделяясь на несколько потоков и сливаясь в один. Далее эти ресурсы снова возникают из небытия в виде готовой продукции, учет которой происходит в бухгалтерии. Остается большой загадкой, что же происходит внутри этого зловещего треугольника, каковы производственные потери, эффективность использования… [1]
Хорошо известно, что традиционно используемые в России бюджетные подходы оперируют со стоимостью потребленных в процессе деятельности ресурсов (материалы, зарплата, электроэнергия, аренда и т.д.). При подсчете себестоимости изготавливаемой на предприятии продукции стоимость потребленных ресурсов распределяется по данным объектам учета. Прямые затраты на материалы и труд можно разнести без особых затруднений, используя очевидную причинно-следственную связь между ними и объектами учета. Сложности возникают при разнесении накладных расходов.
Методы калькуляции полной себестоимости принято объединять в две группы [2]:
- Absorption Costing и ABC-Costing.
- Absorption Costing («Котловой» метод) основан на разнесении косвенных затрат по изготавливаемым продуктам. Он ровесник самого управленческого учета. В России этот метод покрывает не менее 90% всех вычислений себестоимости. Методы разнесения общих затрат просты, но эмпиричны, поэтому неточны. Они оправданны лишь тогда, когда доля косвенных затрат в себестоимости невелика (10-15%). В работе [3] приведена зависимость структуры производственных и накладных расходов от уровня автоматизации производства.

Рис. 1. Изменения структуры затрат по мере внедрения современных техник управления
Из приведенного выше рисунка видно, что с увеличением уровня автоматизации производства доля накладных расходов (постоянные издержки) в себестоимости изготавливаемой продукции значительно возрастает. Сегодня косвенные затраты в автоматизированных производствах составляют примерно 50-60%. Традиционные методы расчета затрат стали терять актуальность.
С начала 1960-х гг. изменения формы производства и ведения бизнеса привели к тому, что традиционный метод учета затрат стали называть «врагом номер один для производства» из-за их весьма сомнительной пользы [2]. Хотя «Котловой» метод и используется обычно для нужд налогового учета, но с точки зрения внутреннего управления неизбежно имеет серьезные недостатки, — это:
- недостаточно точная оценка издержек производства отдельного продукта;
- себестоимость не несет информацию для руководителей предприятия, необходимую для решения главного вопроса "Что делать?".
Ясно также, что, опираясь на «Котловой» метод и применяя только факторы издержек, зависящие от объема производства, для распределения накладных расходов (не зависящих от этого объема), в отчетах можно получить существенные искажения. Степень искажения зависит от доли накладных расходов в общих затратах и от степени диверсифицированности выпускаемой продукции (для выпуска большой номенклатуры изделий различные ресурсы требуются в существенно разном количестве).
ABC-Costing (АВС-анализ). Аббревиатура «ABC» является сокращением полного названия «Activity-Based Costing», что переводится как «расчет себестоимости на основе разнесения затрат по видам деятельности». Временем его появления на Западе считаются 80-е годы. В советской экономической школе данный аппарат был также известен под названием функционально-стоимостного анализа. Методика функционально-стоимостного анализа была разработана для преодоления известных недостатков Absorption Costing — традиционного бухгалтерского подхода к учету затрат и увязывания финансовых результатов с операционной деятельностью предприятия. В основе метода лежит разделение производственного процесса на отдельные задачи, выделение так называемых центров затрат (cost drivers) и расчет требуемых ресурсов (например, время или деньги) для каждого из них. Стоимость рассчитанных ресурсов разносится на конечную продукцию по этим центрам затрат.
Однако вопрос об их соотнесении к производимым изделиям в реальном масштабе времени, все равно, остается открытым, если само производство не работает в соответствие заранее составленным расписанием. Применение MES позволяет составлять и своевременно корректировать детальные производственные расписания [4], что, в свою очередь, дает возможность более точно определить фактическую себестоимость изготовления, как каждой отдельной детали, так и всего изделия в целом.
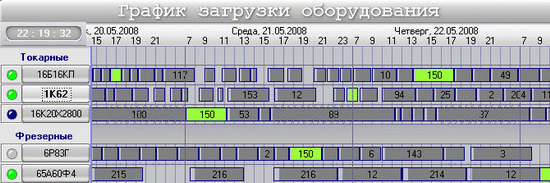
Рис. 2. Вид обрабатываемой детали на диаграмме Гантта
Расписание, составленное MES-системой для обрабатываемых деталей и сборочных единиц, позволяет указать, когда и на каком оборудовании будет выполняться та или иная технологическая операция. С учетом того, что длительность каждой такой операции указана в исходном техпроцессе, можно говорить, что составленное расписание, по существу, формализует последовательность обработки каждой детали в виде некоего «бизнес-процесса». На диаграмме Гантта (на графике загрузки оборудования, рис.2) этот «бизнес-процесс» визуализируется в виде последовательности линий, расположенных напротив используемого для обработки оборудования, длина которых пропорциональна времени выполнения соответствующей технологической операции.
С другой стороны, любой описанный бизнес процесс может быть положен в основу пооперационного метода калькуляции себестоимости, когда накладные расходы привязываются к центрам затрат (cost drivers — в местах использования ресурсов при выполнении работ над изготавливаемыми продуктами). На рис.3. приведены различные схемы калькуляции себестоимости изделий [3], опирающиеся на «котловой» метод и АВС-анализ соответственно.
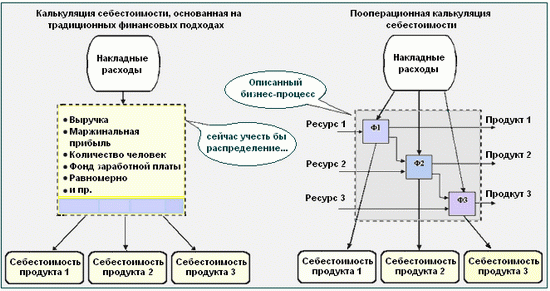
Рис. 3. Различие в подходах к распределению накладных расходов
Функционально-стоимостной анализ требует комбинированного применения процессного (описание бизнес-процессов) и структурного подходов к управлению финансово-хозяйственной деятельностью предприятия. Структурный подход используется, как правило, для получения отдельных исходных данных, необходимых при проведении АВС-анализа. Но оперативное получение этих данных для указанных расчетов в условиях действующих производств — это задача, которую можно решить лишь на основании детального календарного планирования производства, т.е. путем составления и коррекции текущих производственных расписаний. Последняя задача решается на уровне MES систем [4].
Детальное производственное расписание, полученное в MES, является базисом для поведения оперативного АВС-анализа производства. Но для того, чтобы осуществить этот оперативный функционально-стоимостной анализ в реальном масштабе времени, необходимо для каждой детали, входящей в изделие (на диаграмме Гантта, представленной на рис.4, детали одного изделия выделены зеленым цветом), необходимо предварительно определить численные параметры соответствующих центров затрат. Это три основные характеристики для каждого используемого в производственном цикле рабочего места (станка):
- Стоимость станко-часа простоя оборудования;
- Стоимость станко-часа работы оборудования;
- Стоимость станко-часа ремонта оборудования.
Так в приведенном ниже примере для токарно-винторезного станка модели 1К62 указанные значения составляют 45, 340 и 120 рублей соответственно.
Накладные расходы, в состав которых входит
- Амортизация основных фондов,
- Амортизация нематериальных активов,
- Арендная плата,
- Отчисления в ремонтный фонд,
- Вспомогательные материалы,
- Электроэнергия,
- Износ инструмента,
- Зарплата вспомогательных рабочих,
- Отчисления на социальные цели вспомогательных рабочих,
- Зарплата административно-управленческого персонала,
- Отчисления на социальные цели административно-управленческого персонала,
- Командировочные расходы,
- Представительские расходы,
- Затраты на рекламу,
- Налоги на пользование автомобильными дорогами,
- Плата за краткосрочный кредит,
- Прочие расходы,
включаются в этой схеме в стоимость станко-часа простоя оборудования, причем общая сумма накладных расходов, приходящихся на производственное подразделение (цех), распределяется для каждого конкретного станка пропорционально его остаточной стоимости. Т.е. простаивание нового и дорогостоящего оборудования обходится производству значительно дороже. Естественно, что стоимость станко-часа работы оборудования включает в качестве компонента, как затраты на его простой, так и стоимость потребляемой электроэнергии и вспомогательных материалов (например, затраты на используемую смазочно-охлаждающую жидкость и ее регенерацию, амортизацию режущего инструмента и т.п.). Цена станко-часа ремонта традиционно зависит от так называемой категории сложности оборудования.
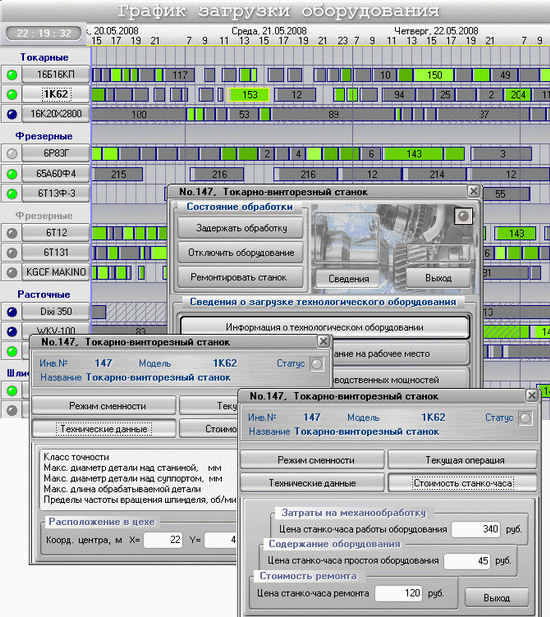
Рис. 4. Структура цены станко-часа для технологического оборудования
Далее расчет стоимости каждой выполняемой технологической операции осуществляется не только путем традиционного умножения стоимости станко-часа работы на время этой технологической операции, а к указанному произведению еще добавляется и цена вынужденных простоев станка (в ожидании начала этой операции), а также стоимость возможного ремонта, если таковой предшествовал ее началу. Возможен также вариант равномерного распределения затрат, связанных с выполняемым ремонтом, на все операции, которые на данном оборудовании выполнялись.
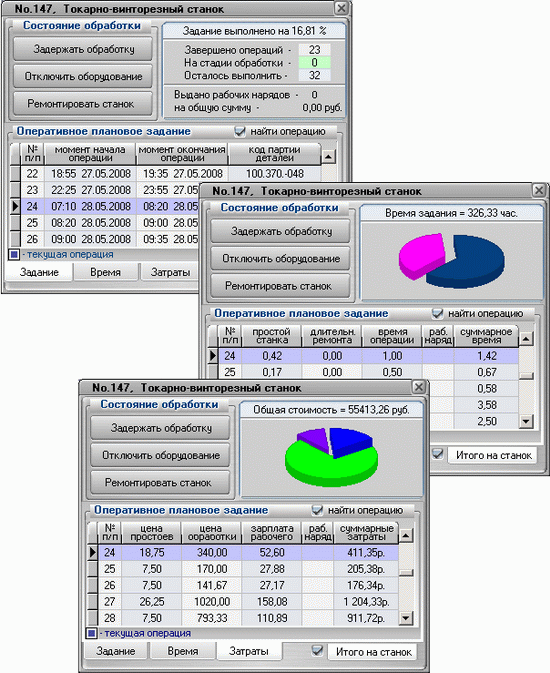
Рис. 5. Пример пооперационного вычисления затрат, связанных с рабочим местом
Поскольку производственный заказ представляет собой, как правило, целый комплект изготавливаемых деталей и сборочных единиц (ДСЕ), то общая его себестоимость определяется суммарными затратами на обработку каждой входящей в него детали (на диаграмме Гантта, представленной на Рис.4, все операции, связанные с обработкой ДСЕ одного заказа выделены зеленым цветом). Кроме того, диспетчерский модуль MES систем (DPU) дает возможность проводить On-line контроль обработки всех ДСЕ, как по каждому заказу, так и по отдельным центрам затрат, т.е. по используемому технологическому оборудованию (Рис.5).
Составление отчета о себестоимости заказа завершает ее калькуляцию в MES, опирающуюся на ABC-анализ (Рис.6). Его целью является обобщение информации о собранных для выполнения конкретного заказа затратах (как в общей сумме, так и в разрезе элементов затрат). Причем в отчете о себестоимости присутствуют как плановые данные по затратам, так и фактические, что позволяет использовать отчет для оценки работы подразделений и контроля затрат по конкретному заказу.
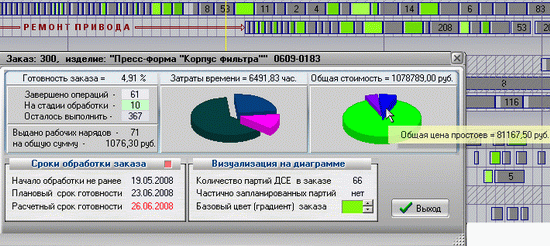
Рис. 6. Оперативная калькуляция себестоимости обработки заказа
Более того, в реальном масштабе времени MES-система визуализирует пользователю текущий процент выполнения заказа (число завершенных и оставшихся операций), а также текущие производственные затраты вплоть до указания цены простоев оборудования, связанных с ожиданием начала обработки ДСЕ от данного заказа.
В заключение отметим, что оперативный функционально-стоимостной анализ производства реализуем на уровне MES-систем. Это способствует сопоставлению затрат по отдельным заказам, дает возможность выявить наиболее рентабельные заказы как в целом, так и по отдельным операциям в аналогичных заказах.
Следовательно, внедряя MES в производство, руководство предприятия дополнительно получает в свои руки реальный инструмент для принятия надлежащих управленческих решений.
ЛИТЕРАТУРА
- С.Бежин, "12 смертельных финансовых грехов, или время настроить инструменты".
- А.Мицкевич, "Когда «котловой» учет правит бал...".
- С.Ковалев, "Функционально-стоимостной анализ бизнес-процессов".
- Е.Фролов, Р.Загидуллин, "MES-системы. Вид «сверху», взгляд изнутри". Генеральный директор, №4, 2008.
Об авторе:
Евгений Борисович Фролов, д.т.н., профессор, Московский государственный технологический университет "СТАНКИН", кафедра "Информационные технологии и вычислительные системы".
|
 |